
Mercedes-Benz Cars broke ground on a new factory on its home ground in Sindelfingen outside of Stuttgart that the automaker claims will be the most modern production center in the world when it opens in 2020.
“Our ‘Factory 56’ will define a new way of building cars. With its ‘Factory 56’, Mercedes-Benz Cars is creating the car plant of the future,” said Markus Schäfer, member of the Divisional Board of Mercedes-Benz Cars, Production and Supply Chain.
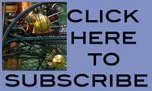
“It combines three trend-setting features: It is consistently digital and flexible – and it brings the term ‘green production’ to life. As the inventor of the car, we are reinventing production.”
In 2020, the “Factory 56” will start production of upper- and luxury-class cars and electric vehicles, including passenger cars, electric vehicles of the upper and luxury class and robo-taxis.
The announcement comes as competition and contention are on the rise. BMW is spending $600 million to increase production at its plant in South Carolina that builds the company’s popular sport-activity vehicles by about 35,000 units.
(BMW rolls into Geneva with multiple debuts. Click Here for the story.)
Building a new plant in Germany is an interesting proposition, as German unions are in negotiations with automakers. It’s unclear how the early concessions unions have secured, such as shorter work weeks and pay increases, will impact the new plant.
Among the various vehicles the new factory is slated to build is the new generation of Mercedes-Benz’s signature vehicle, the S-Class, as well as the first electric vehicle of the new all-electric EQ brand.
The plant itself is immense covering for than 220,000 square meters and will require approximately 6,400 tons of steel for the construction – almost as much as used in the Eiffel Tower.
The employees work at ergonomically optimized workstations that are supported in their tasks by digital tools. The focus is on the use of intelligent, flexible technology.
(Click Here for a first-look at the new BMW X4.)
A new work organization provides for more flexible and modern working-time models. The plant will include sophisticated digitally supported processes including work organization as well as logistics and quality assurance.
In the future, for example, the finished vehicles shall drive off the line automated to the loading station. Under “Digital Anticipation” in the Mercedes me App and online, customers purchasing new vehicles can already today gain exclusive insights into the production of their vehicles and thus have a much more enjoyable wait for delivery, the company noted.
In the assembly area driverless transport systems with product baskets support logistics in the assembly and ensure the supply of the required materials for the employees at the line. Radio Frequency Identification-technologies are integrated into “Factory 56” so components and vehicles can be digitally tracked and linked with one another.
Artificial Intelligence, Big Data analyses and Predictive Maintenance guarantee high transparency and support in production planning, control and also in quality assurance. Through the analysis of existing production data, for instance, predictions on potential faults or due maintenance work can be made in advance.
(To see more about BMW’s new partnership to develop EV batteries, Click Here.)
The Blue Sky architecture supports a pleasant working climate for the employees in daylight. In addition, the temperature of the hall can be set at up to seven degrees below the outside temperature.